Kitchen cabinets often come with a hefty price tag, leaving homeowners puzzled about the reasons behind their high cost.
This article delves into the intricacies of cabinet pricing, examining factors such as material expenses, labor costs, and additional functionalities that contribute to their expense.
From the type of wood used to the intricacy of hardware, each aspect plays a crucial role in determining the final price. Understanding these factors can help homeowners navigate their kitchen renovation budgets more effectively.
The Anatomy of a Cabinet: Breaking Down the Components
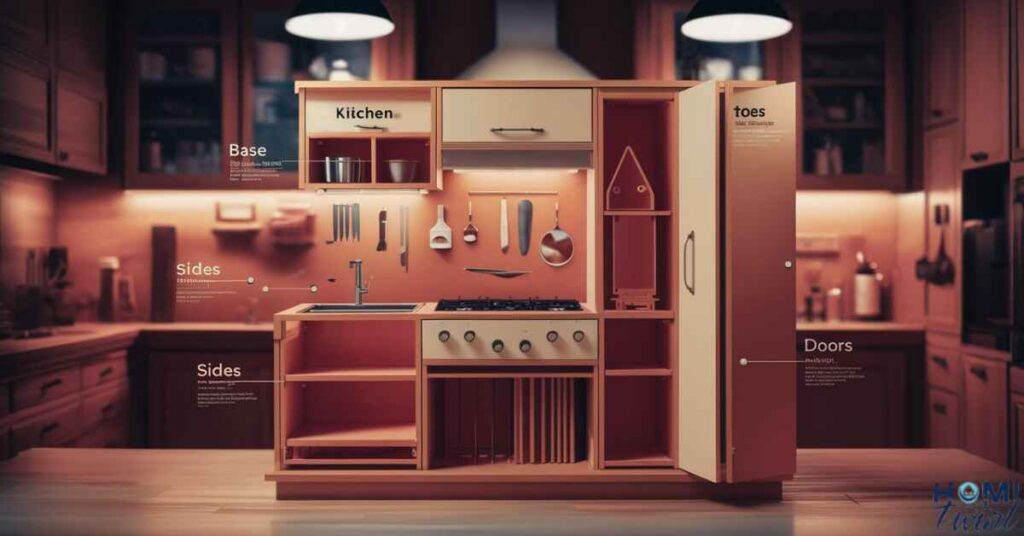
Behind the sleek exteriors of kitchen and bathroom cabinets lies a complex structure designed for both functionality and durability. Let’s break down the key components that drive up the cost.
- Cabinet boxes: The foundation of any cabinet is its box, typically constructed from solid wood or high-quality plywood. These materials ensure long-lasting strength and resistance to warping or sagging over time. The cost of these materials can vary significantly based on the type of wood used, with hardwoods like oak, maple, and cherry commanding higher prices than softwoods or engineered wood products.
- Shelves and drawers: Customizable shelves and drawers allow for efficient storage solutions tailored to your needs. From pull-out shelves to deep drawers, these features add both convenience and cost. The more intricate the design and the higher the quality of the hardware used, the higher the overall cost.
- Door and drawer fronts: The visible face of your cabinets, the door and drawer fronts, contribute significantly to the overall aesthetic. Style, material, and hardware choices can quickly escalate costs. Solid wood door fronts, particularly those made from exotic or rare woods, can be substantially more expensive than those made from less expensive materials like particleboard or melamine.
- Finishes: From rich stains to vibrant paints, the finishing touches on your cabinets are what truly bring them to life. Premium finishes, often applied by skilled artisans, add both beauty and longevity, but at a higher price point. Specialty finishes, such as glazes, distressing, or hand-rubbed techniques, can further increase the cost due to the additional labor and materials involved.
Read This Blog: HOW TO MEASURE MEDICINE CABINET
Quality Craftsmanship: The Backbone of Expensive Cabinets
Behind every high-end cabinet lies the expert craftsmanship of skilled professionals. This attention to detail and precision comes at a premium.
- Skilled labor: From precise cutting and assembly to flawless finishing, experienced cabinetmakers command higher wages for their expertise. The labor costs associated with custom cabinetry can account for a significant portion of the overall cost, as each cabinet is meticulously crafted to meet specific design specifications.
- Custom cabinetry: Tailored designs for unique spaces, such as awkward corners or angled walls, require meticulous planning and execution, driving up costs. Custom cabinets are often built to order, with each component carefully measured and cut to fit the specific dimensions of the space, resulting in higher labor and material costs.
- Small-batch production: Unlike mass-manufactured cabinets, custom and semi-custom options are produced in smaller quantities, with greater quality control and attention to detail, justifying their higher price points. This small-batch production process allows for more personalized attention to each cabinet, resulting in a higher-quality finished product.
Case Study: The Cost of Custom Cabinets
To illustrate the potential cost of custom cabinetry, let’s consider a hypothetical kitchen remodel project. For a medium-sized kitchen with 25 linear feet of cabinets, the cost of custom cabinets made from high-quality solid wood, such as cherry or maple, could range from $15,000 to $30,000 or more, depending on the specific design elements, hardware, and finishes chosen.
In contrast, stock or semi-custom cabinets for the same kitchen size could cost anywhere from $5,000 to $15,000, depending on the materials and options selected. While the upfront cost of custom cabinets is significantly higher, many homeowners view it as a worthwhile investment for the tailored fit, unique design, and superior craftsmanship.
The Material Matters: Exploring Premium Options
The materials used in cabinet construction play a significant role in determining their cost. While budget-friendly options exist, premium materials command a higher price tag for their durability, rarity, and aesthetic appeal.
- Solid wood: Classic choices like oak, maple, and cherry are renowned for their strength and timeless beauty, making them popular yet pricier options. The cost of solid wood cabinets can vary significantly based on the specific wood species, with some exotic or rare woods being substantially more expensive than domestic hardwoods. Here’s a breakdown of some common solid wood options and their approximate costs per linear foot:
- Oak: $150 – $300
- Maple: $200 – $400
- Cherry: $300 – $600
- Walnut: $400 – $800
- Teak: $600 – $1,200
- Exotic woods: For a true touch of luxury, exotic woods like teak and zebrawood offer unique grains and colors, but come with a premium price tag due to their rarity and importation costs. These exotic wood options can range from $800 to $2,000 or more per linear foot, depending on the specific wood species and cabinet design.
- Engineered wood: More cost-effective alternatives like plywood and particle board provide a balance between affordability and functionality, though they may lack the warmth and character of solid wood. Plywood cabinets typically range from $100 to $300 per linear foot, while particle board options can be even more affordable, starting around $50 per linear foot.
Also Read This Blog: HOW TO ORGANIZE SPICES IN CABINET
It’s important to note that the cost of materials can vary significantly based on factors such as the cabinet manufacturer, the specific design elements, and the region or market in which you’re purchasing the cabinets.
Hardware and Accessories: The Icing on the Cake
While the cabinet boxes and doors are the main components, the hardware and accessories you choose can also significantly impact the overall cost:
- Drawer glides and hinges: Soft-close, full-extension mechanisms ensure smooth operation but come at a higher price point. High-quality drawer glides and hinges can add $50 to $100 or more per cabinet, depending on the specific hardware selected.
- Cabinet organizers: Maximize storage efficiency with pull-out shelves, lazy Susans, and other organizational tools, adding both convenience and cost. These organizational accessories can range from $50 to $300 or more per cabinet, depending on the complexity and materials used.
- Decorative elements: Glass inserts, corbels, and other decorative touches can elevate the aesthetic appeal of your cabinets while increasing the bottom line. Glass inserts, for example, can add $100 to $300 or more per cabinet door, depending on the size and complexity of the design.
Customization: The Key to Unlocking Value
One of the primary reasons for the high cost of cabinets is the ability to tailor them to your specific needs and preferences. Customization adds both functionality and aesthetic value, but also increases the overall cost:
- Custom sizing: Ensuring a precise fit for awkward spaces or unique room dimensions requires precise measurements and customized construction. Custom sizing can add anywhere from 25% to 50% or more to the overall cost of the cabinets, depending on the complexity of the space and the level of customization required.
- Layout and design: Optimizing the layout and design of your cabinets for efficient workflow and functionality is a service provided by skilled designers, adding to the overall cost. Professional design services can range from $500 to $2,000 or more, depending on the scope of the project and the designer’s experience and reputation.
- Finishes and styles: From traditional Shaker styles to sleek, modern looks, customizing the finish and style of your cabinets to match your personal aesthetic preferences comes at a premium. Custom finishes, such as glazes, distressing, or hand-rubbed techniques, can add hundreds or even thousands of dollars to the cost of your cabinets, depending on the complexity of the finish and the amount of labor required.
Installation and Delivery: The Hidden Costs
Even after the cabinets themselves are accounted for, additional costs can arise during the installation and delivery process.
- Professional installation: Ensuring a flawless installation often requires the expertise of professional contractors, adding labor costs to the equation. Professional installation costs can range from $50 to $200 or more per linear foot of cabinets, depending on the complexity of the installation and the region in which you live.
- Delivery and setup: The safe transportation and careful placement of your new cabinets may incur additional fees,
Installation and Delivery: The Hidden Costs
- Delivery and setup: The safe transportation and careful placement of your new cabinets may incur additional fees, especially for larger or complex orders. Delivery fees can range from a few hundred dollars for local deliveries to several thousand dollars for long-distance shipments, depending on the size and weight of the order.
In addition to the delivery costs, some cabinet manufacturers or retailers may charge additional fees for services such as uncrating, debris removal, and on-site assembly or installation of the cabinets.
Investing in Longevity: The Lifetime Value of Cabinets
While the upfront cost of high-quality cabinets may seem steep, it’s important to consider their long-term value and potential return on investment.
- Durability and wear resistance: Premium materials and construction techniques ensure your cabinets can withstand the rigors of daily use for decades. Well-constructed solid wood cabinets, when properly maintained, can last for 50 years or more, making them a wise long-term investment.
- Timeless designs: Well-crafted cabinets with classic styles and finishes can maintain their aesthetic appeal for years, avoiding the need for frequent replacements. This longevity can help offset the higher upfront cost over time, as you won’t need to invest in a complete cabinet overhaul as frequently.
- Value-added resale potential: High-end cabinets are often a selling point for potential homebuyers, potentially increasing your property’s resale value. According to a recent study by Remodeling Magazine, a minor kitchen remodel, which typically includes cabinet refacing or replacement, can recoup up to 77.6% of the cost when selling the home.
Case Study: The Long-Term Value of Premium Cabinets
Consider this example: You invest $25,000 in custom, solid wood cabinets for your kitchen remodel. With proper care and maintenance, these cabinets could easily last 30 years or more. In contrast, lower-quality, mass-manufactured cabinets costing $10,000 may need to be replaced every 10-15 years due to wear and tear or changing design trends.
Over a 30-year period, you’d likely need to replace the lower-cost cabinets twice, resulting in a total cost of $30,000 or more. Additionally, the higher-quality cabinets can potentially increase the resale value of your home, helping to offset the initial investment.
While the upfront cost may be higher, investing in premium cabinets can pay dividends in the long run through their durability, timeless appeal, and potential to enhance your home’s value.
The Impact of Kitchen Remodeling Expenses and Custom Cabinetry
When planning a kitchen renovation, cabinetry costs often account for a significant portion of the overall kitchen remodeling expenses. In fact, according to a report by Remodeling Magazine, cabinet replacement or refacing can make up 25% to 40% of the total cost of a minor or major kitchen remodel.
For homeowners seeking a truly personalized and functional kitchen space, custom cabinetry is often the preferred choice. However, this level of customization comes at a premium price point. Custom cabinets are built to order, allowing for precise measurements, unique designs, and tailored features that mass-manufactured options simply cannot match.
While the initial investment in custom cabinetry may be higher, many homeowners view it as a worthwhile expense for the following reasons:
- Optimized use of space: Custom cabinets can be designed to maximize every inch of available space, incorporating clever storage solutions and maximizing functionality in even the most challenging layouts.
- Unique design elements: From intricate woodworking details to specialty finishes and hardware, custom cabinets offer virtually limitless design possibilities, allowing you to create a truly one-of-a-kind kitchen that reflects your personal style.
- Improved resale value: High-quality, custom cabinets are often a major selling point for potential homebuyers, as they add both aesthetic appeal and functional value to the kitchen space. This can help increase your home’s resale value and make it more attractive to buyers.
- Longevity and durability: Custom cabinets are typically constructed from premium materials and built with meticulous attention to detail, ensuring they can withstand the rigors of daily use for decades without showing signs of wear or degradation.
While the upfront cost of custom cabinetry can be substantial, ranging from $15,000 to $50,000 or more for a typical kitchen, many homeowners view it as a long-term investment in their home’s function, beauty, and resale value.
The Pros and Cons of Mass-Manufactured Cabinets
On the opposite end of the spectrum from custom cabinetry are mass-manufactured cabinets, which offer a more cost-effective option for those working with tighter budgets. While these pre-fabricated cabinets may lack the personalized touch and premium materials of their custom counterparts, they can still provide a functional and aesthetically pleasing solution for kitchen renovations.
Pros of Mass-Manufactured Cabinets:
- Affordability: One of the most significant advantages of mass-manufactured cabinets is their lower price point. These cabinets are produced in large quantities, which helps to reduce manufacturing costs and makes them more accessible to a wider range of homeowners.
- Availability: Mass-manufactured cabinets are widely available at most home improvement stores and online retailers, making them a convenient option for those working on tight timelines or in remote areas.
- Consistent quality: While not as customized as their handcrafted counterparts, mass-manufactured cabinets are subject to strict quality control measures, ensuring a consistent level of quality across the board.
- Ease of installation: Many mass-manufactured cabinet systems are designed for easy installation, with pre-cut components and straightforward assembly instructions, making them a viable option for DIY renovations.
Cons of Mass-Manufactured Cabinets:
- Limited customization: One of the most significant drawbacks of mass-manufactured cabinets is their lack of customization options. These cabinets are produced in standardized sizes and styles, limiting the ability to tailor them to unique spaces or personal preferences.
- Lower-quality materials: To keep costs down, mass-manufactured cabinets are often constructed from lower-quality materials, such as particle board or laminate, which may not have the same durability or aesthetic appeal as solid wood or premium materials.
- Shorter lifespan: Due to the lower-quality materials and mass production processes, mass-manufactured cabinets may have a shorter lifespan compared to their custom counterparts, potentially requiring replacement or refacing more frequently.
- Limited resale value: While mass-manufactured cabinets can provide a functional and aesthetically pleasing solution for a kitchen renovation, they may not add as much resale value to a home as custom cabinetry, which is often seen as a more desirable and long-term investment.
When deciding between mass-manufactured and custom cabinets, it’s essential to weigh your budget, design preferences, and long-term goals for your kitchen space. While mass-manufactured cabinets offer a more affordable option, custom cabinetry may provide a better return on investment for those seeking a truly personalized and long-lasting solution.
The Role of Labor Expenses in Cabinet Renovation
While the cost of materials is a significant factor in the overall expense of cabinet installation or renovation, labor expenses can also contribute substantially to the final price tag. The level of expertise required, the complexity of the project, and the region in which the work is being performed can all impact the labor costs associated with cabinet work.
- Installation labor: The installation of cabinets, whether new or refaced, requires precision and attention to detail. Professional cabinet installers typically charge hourly rates ranging from $50 to $100 or more, depending on their experience and location. For a typical kitchen renovation, installation labor costs can range from $1,000 to $5,000 or more.
- Removal and disposal: Before new cabinets can be installed, the existing cabinetry must be carefully removed and disposed of. This process can be time-consuming and labor-intensive, especially in older homes or spaces with intricate cabinetry layouts. Removal and disposal costs can range from a few hundred dollars for smaller projects to several thousand dollars for larger, more complex jobs.
- Carpentry work: In some cases, additional carpentry work may be required to prepare the space for new cabinets. This can include tasks such as repairing or reinforcing walls, leveling floors, or building out new structures to accommodate custom cabinet designs. Skilled carpenters can charge hourly rates ranging from $50 to $150 or more, depending on the complexity of the work and the region.
- Finishing and customization: For custom cabinets or those requiring specialized finishes or detailing, additional labor costs may be incurred for skilled art.
Frequently Asked Question
Why are kitchen cabinets expensive?
Kitchen cabinets are expensive due to factors like the cost of materials, labor for manufacturing and installation, and additional features like specialized hardware.
What materials contribute to the high cost of cabinets?
Materials like oak, cherry, and maple are commonly used for cabinets, with prices varying based on wood type and quality.
How can homeowners reduce the cost of kitchen cabinets?
Homeowners can opt for less expensive wood options, choose simpler designs, shop around for deals, consider DIY options, and refurbish existing cabinets instead of replacing them entirely.
Are custom cabinets always more expensive than pre-made ones?
Custom cabinets tend to be more expensive due to their tailored designs and higher quality materials, whereas pre-made cabinets offer more affordable options with limited customization.
What role does labor play in cabinet pricing?
Labor costs encompass both manufacturing and installation, with custom cabinets requiring more intricate craftsmanship and thus being more expensive to produce and install.
Do shipping and delivery impact cabinet costs?
Yes, shipping and delivery costs can significantly contribute to the overall expense, especially for heavy and bulky cabinet materials, with distances from manufacturers affecting the final price.
Conclusion
the costliness of kitchen cabinets stems from a multitude of factors, including the choice of materials, intricacy of design, labor-intensive manufacturing processes, and additional functionalities.
While expensive cabinets may initially cause sticker shock, homeowners can navigate this aspect of kitchen renovations by exploring cost-saving options such as opting for more affordable wood types, simplifying designs, and considering DIY refurbishment projects. Moreover, being mindful of regional pricing disparities and seeking out deals from various retailers can further help mitigate expenses.
By understanding the nuances of cabinet pricing and making informed decisions, homeowners can strike a balance between quality, functionality, and budget, ensuring that their kitchen remodeling endeavors are both aesthetically pleasing and financially feasible.